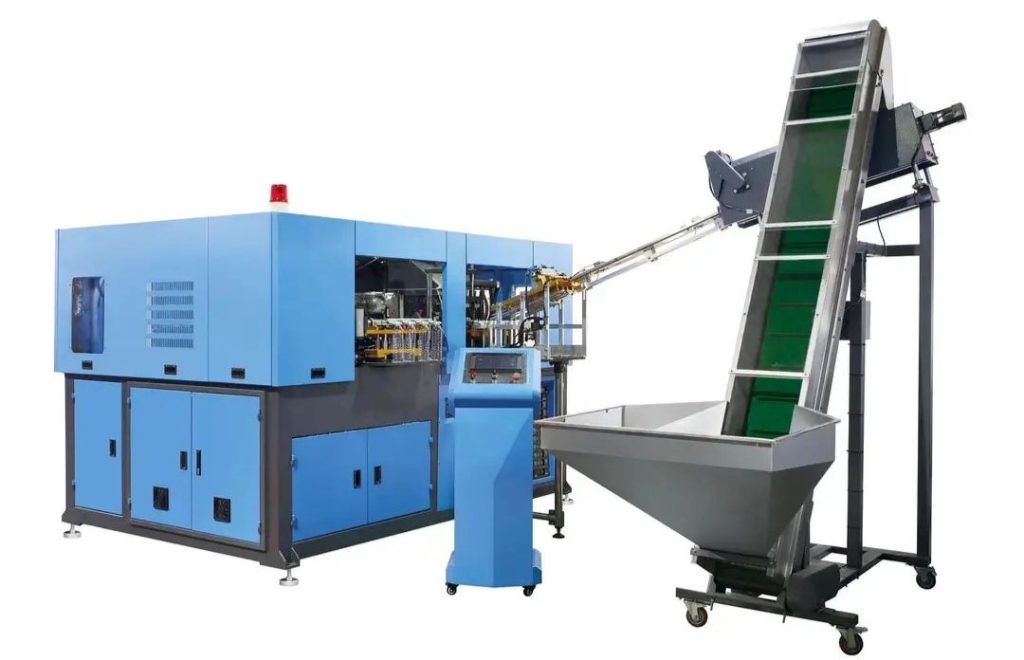
Imagine baking a cake: you follow the recipe, set the oven, and wait. But when you check, the cake is unevenly baked or has bubbles. Frustrating, right? Similarly, in the world of plastic manufacturing, PET preform molding machines can sometimes produce less-than-perfect results. But don’t worry! Just like tweaking your baking process, understanding and addressing common issues in PET preform molding can lead to better outcomes.
In this guide, we’ll delve into the typical problems faced during PET preform molding and provide straightforward solutions to help you achieve optimal results.
1. Understanding PET Preform Molding Machines
PET (Polyethylene Terephthalate) is a type of plastic commonly used for packaging, especially for beverages. PET preform molding machines are specialized equipment designed to produce preforms, which are then blown into bottles.
These machines operate by injecting molten PET into molds to form preforms. The precision and efficiency of these machines are crucial for producing high-quality bottles.
2. Importance of Quality in PET Preform Production
Quality in PET preform production ensures:
- Product Integrity: Prevents leaks and contamination.
- Cost Efficiency: Reduces waste and rework.
- Customer Satisfaction: Delivers consistent and reliable products.
Maintaining high-quality standards is essential for brand reputation and operational efficiency.
3. Common Issues and Their Solutions
3.1. Surface Defects (Flow Marks, Bubbles, Haze)
- Causes:
- Inconsistent cooling rates.
- Moisture in the resin.
- Improper mold temperature.
- Solutions:
- Ensure uniform cooling by maintaining consistent mold temperatures.
- Dry the PET resin adequately before processing.
- Adjust injection speed and pressure to optimize flow.
3.2. Yellowing of Preforms
- Causes:
- Overheating of PET resin.
- Prolonged residence time in the barrel.
- Solutions:
- Optimize barrel temperature settings.
- Reduce the residence time by adjusting cycle times.
3.3. Dimensional Inaccuracies
- Causes:
- Worn-out molds.
- Inconsistent injection pressure.
- Solutions:
- Regularly inspect and maintain molds.
- Calibrate injection parameters for consistency.
3.4. Cracking or Brittleness
- Causes:
- Rapid cooling.
- Excessive stress during ejection.
- Solutions:
- Gradually cool the preforms to relieve internal stresses.
- Adjust ejection mechanisms to minimize force.
3.5. Incomplete Filling (Short Shots)
- Causes:
- Insufficient injection pressure.
- Blocked vents.
- Solutions:
- Increase injection pressure.
- Clean and maintain venting systems.
4. Preventive Maintenance Tips
- Regular Cleaning: Prevents buildup of residues that can affect product quality.
- Scheduled Inspections: Early detection of wear and tear.
- Calibration: Ensures machines operate within optimal parameters.
- Training: Equip operators with knowledge to identify and address issues promptly.
5. Conclusion
Just like perfecting a recipe requires understanding and adjustments, achieving excellence in PET preform production hinges on recognizing common issues and implementing effective solutions. By maintaining equipment, monitoring processes, and training personnel, manufacturers can ensure consistent quality and efficiency.
6. FAQs
Q1: Why is my PET preform turning yellow?
A: Yellowing often results from overheating or prolonged residence time in the barrel. Adjusting temperature settings and reducing cycle times can help.
Q2: How can I prevent surface defects on preforms?
A: Ensure uniform cooling, proper drying of resin, and optimal injection parameters to minimize surface imperfections.
Q3: What causes cracks in PET preforms?
A: Rapid cooling and excessive ejection force can lead to cracks. Gradual cooling and gentle ejection can mitigate this.
Q4: Why are my preforms not filling completely?
A: Incomplete filling can be due to low injection pressure or blocked vents. Increasing pressure and cleaning vents can resolve this.
Q5: How often should I maintain my PET preform molding machine?
A: Regular maintenance schedules vary, but a monthly inspection and cleaning routine is a good starting point.
By understanding the intricacies of PET preform molding and proactively addressing common issues, manufacturers can ensure high-quality production and operational efficiency.